21.12.15
Crossrail tunnel fit-out on track
Source: RTM Dec/Jan 16
Gregg Purcell, Crossrail’s railway systems construction manager, discusses the early learning from the complex task of fitting out the new £14.8bn railway’s tunnels.
Back in June 2015 the Crossrail team reached a major milestone by completing its three-year tunnelling activities. The focus has now shifted to the complex task of fitting out the new tunnels and stations along the £14.8bn east-west railway. This includes the installation of track, tunnel ventilation, high voltage power, traction power, signalling, communications and overhead line equipment.
RTM caught up with Gregg Purcell, Crossrail’s railway systems construction manager, who told us the team is starting to “get into stride with their production”.
The overall fit-out includes laying five different types of track – predominantly standard track slab – in the tunnels, using a bespoke fleet of four multi-purpose gantries (MPGs) to carry and locate the track, and using a 465-m long concreting train. The contractor undertaking the Crossrail railway systems main works, contract C610, is ATC – a joint venture comprising Alstom, Transports Sud Ouest (TSO) and Costain Limited.
Just before Christmas, Crossrail said more than 5km of new track had been installed in the eastern section of Crossrail’s tunnels.
When RTM spoke to Purcell, he said: “Early in 2016 we will have concreted all the track from Plumstead up to Victoria Dock Portal on the eastbound side.
“We then switch our attentions to concreting all the westbound track and at that point in time, late January, we then head into the tunnels from Victoria Dock Portal and start pulling rail up towards Stepney Green. We then follow soon behind that in February and March with sleeper installation and concreting work.”
The two main temporary logistics centres for Crossrail’s railway systems are located at Plumstead in south east London and Westbourne Park in west London. Plumstead is the larger of the two railheads with a total of eight tracks, an overhead gantry crane to supply engineering trains and an operations centre to co-ordinate the activity.

MPGs
Most of the track in the central section (80%) is formed from standard track slab, which will connect with the other track forms used at specific locations. A total of 41.2km of standard track slab will be installed on Crossrail using fibre reinforced concrete. The remaining 20% of track will vary between direct-fixed track and a variety of tracks designed to reduce noise and vibration on sensitive parts of the route.
To carry out the initial work, Crossrail is using four MPGs to transport and position approximately 70,000 sleepers in the railway’s central section.
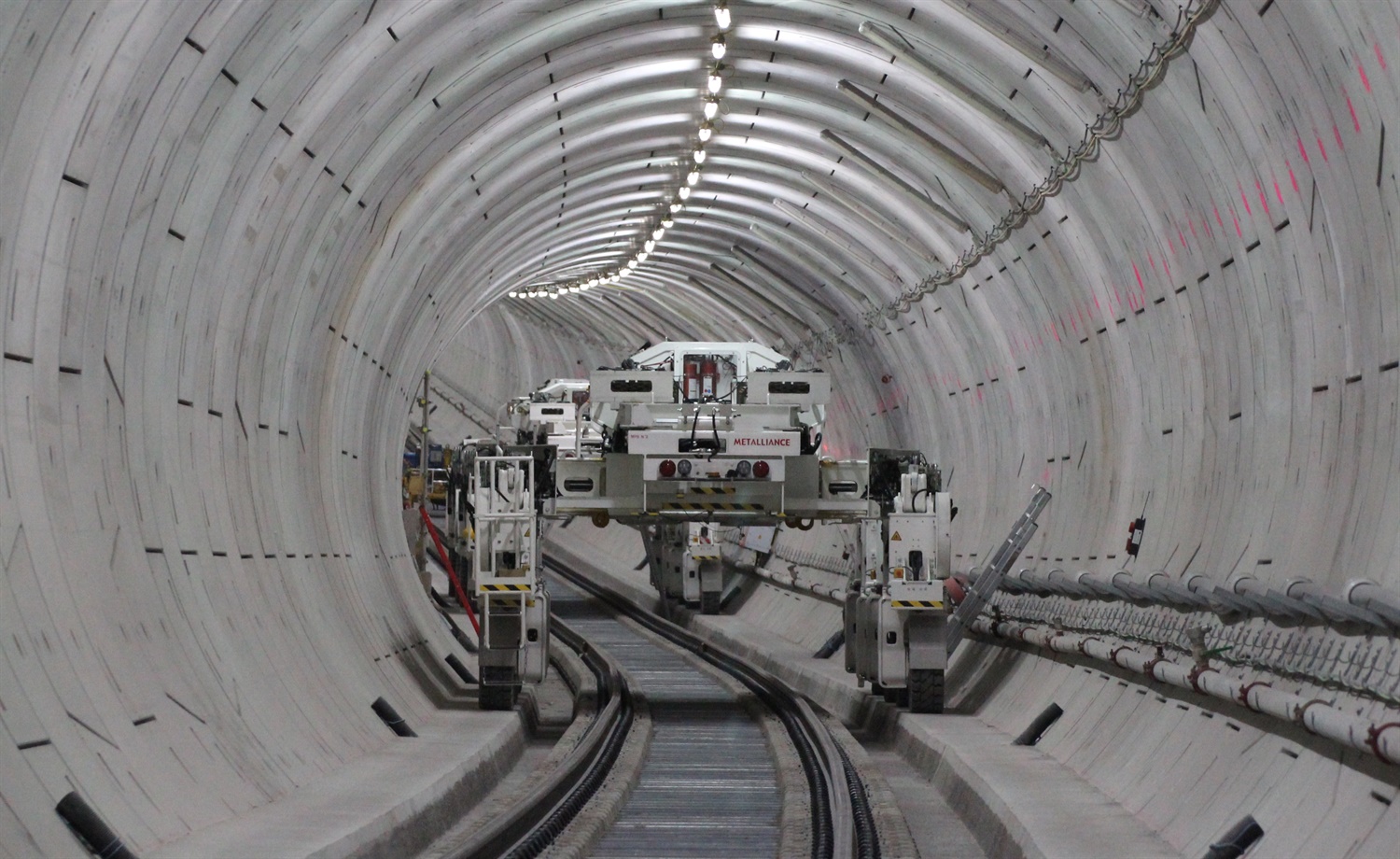
Discussing the MPGs, which have been manufactured for Crossrail by Metalliance in France, Purcell said: “It is a very clever piece of kit. The MPGs we are using are almost like a Mark II version of the MPG which was used on the Channel Tunnel Rail Link [now known as HS1]. A lot of the people we have in our team have a lot of skillset from the C576 contract.
“The MPG that they used in the Thames Tunnels, we are using a variation on that machine. But this is completely bespoke for Crossrail, but we have taken a lot of the best practice and lessons learned. We have put that into the new design.
“Similar to bringing out a new car, we have changed a lot of kit like the wheel configuration, the tyre size, size of the driver’s cab, and we have changed the switches for the various components. A lot of refinement has gone on and it is proving and yielding dividends at the moment.”
He added that all four MPGs are onsite in various positions and configurations. However, one of the early challenges was building up the knowledge base within the ATC team to use the MPGs.
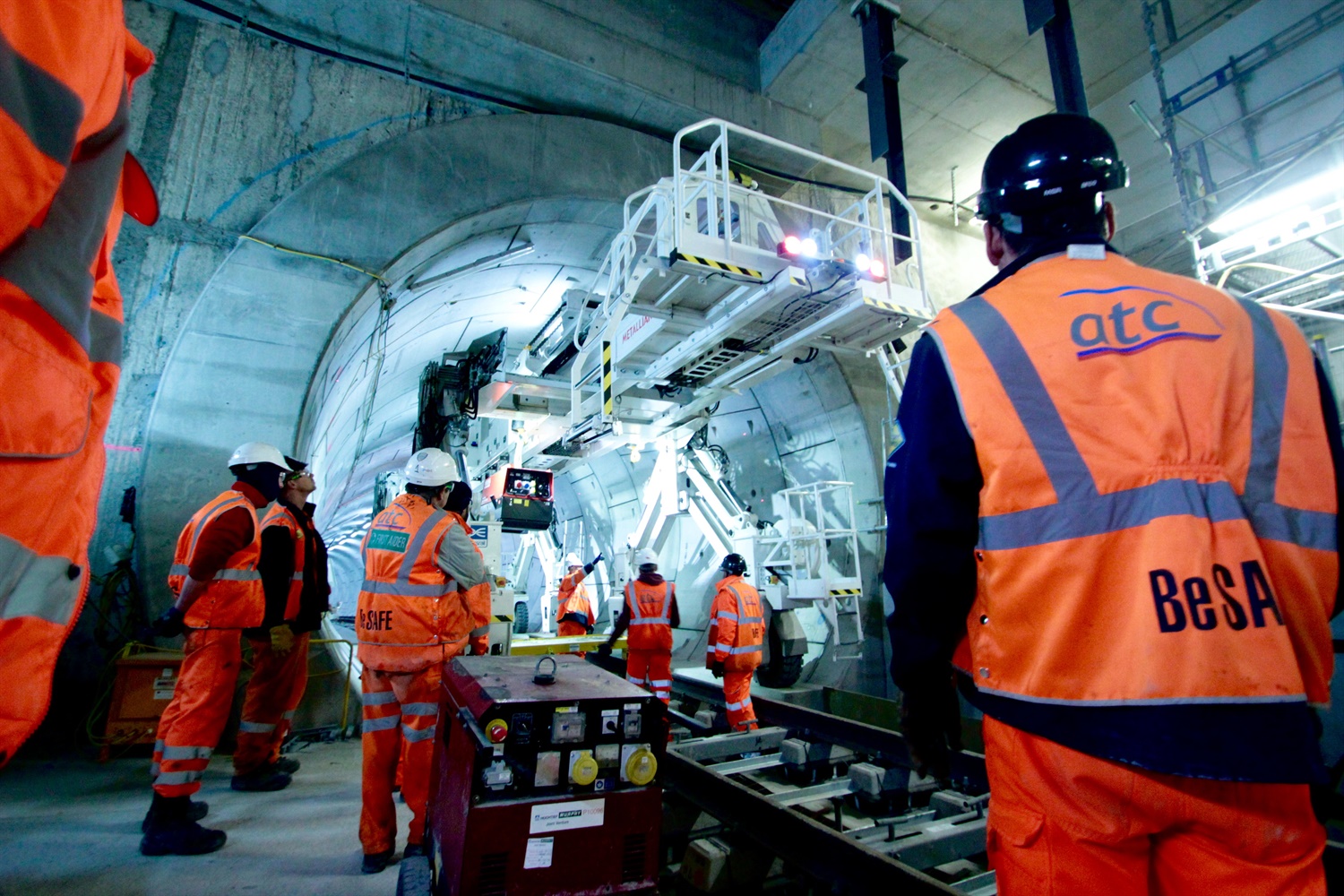
“The way we dealt with this was to send people to the factory in France, who got trained up by the manufacturers. They got to use it in a non-operational environment,” said Purcell.
After positioning 108m-long sections of rail along a stretch of tunnel, the gantry then carries and deposits sleepers at carefully measured intervals, before lifting the rail into place on top of them. The track is then secured in place using clips, props and jigs before it is welded and the formation is concreted into position.
“The sleeper installation on a straight set of track is fairly simple because the jigs that we have actually set the sleepers are at pre-determined spacing,” said Purcell. “The problems we have had with the sleeper spacing early on is that when we go around the curves, the Crossrail curves are fairly tight in the tunnel.
“We have had to perfect our method. We ended up having to regulate the sleepers around the curves. That is one thing we have learnt.” The ATC team has also spent a lot of time speeding up the three-stage process of picking up the track, transporting it and putting it into its final alignment.
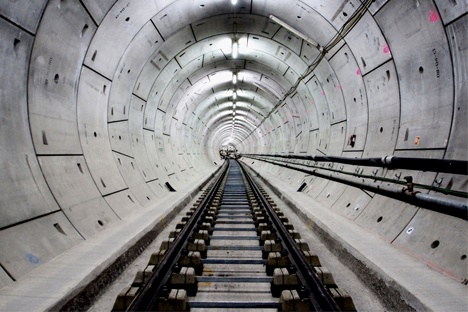
Track forms
When RTM spoke to Purcell, the team had worked on two of its five track forms and was in the process of bringing a third online.
“Starting from the beginning, we have the direct fixed-track,” he said, which has been used within Connaught Tunnel. “We completed that work between January and August 2015.”
Using this track form has allowed engineers to create a flat surface on top of undulations in the ground and to work within the height restrictions that are a feature of the tunnel. A total of 2.6km of direct-fixed track has already been installed on Crossrail.
But most of the track in the central section is formed from standard track slab, though one area uses HAS (high attenuation sleepers) to reduce noise and vibration.
Purcell explained: “The standard slab track is, effectively, a series of concrete blocks joined together by a stainless steel bar. The HAS is similar to that which you see on the Network Rail system, and that is then shrouded in a rubber boot to reduce noise.”
The project also has areas of floating track slab (light) to be used between Tottenham Court Road and Bond Street to minimise noise and vibration impacts from the operating railway on nearby recording studios and hotels, which is a requirement of the Crossrail Act.
The track slab floats on a combination of elastomet rubber bearings and heavy duty springs, and is then jacked up to accommodate the bearings and springs.
When RTM spoke to Purcell in late December 2015, the ATC team had just commenced with building floating slab track (light) under Soho.
Floating track slab (heavy), which sits on heavy duty springs, is to be used in the Farringdon area due to the close proximity of the Barbican. Due to the extra depth added by the spring base of the floating track, a shallower sleeper is needed. To ensure that the shallower sleeper remains durable a dense concrete called MagnaDense is used.
Concreting
Purcell noted that during the track installation there are eight different workfaces open. “At the head of the snake, if you like, we have got the rail pulling activities,” he said. “We have eight different work gangs – made up of eight to 12 workers – from pulling rail through to laying sleepers, to setting track through to aligning, surveying and concreting the track, plus the post-concreting work.”
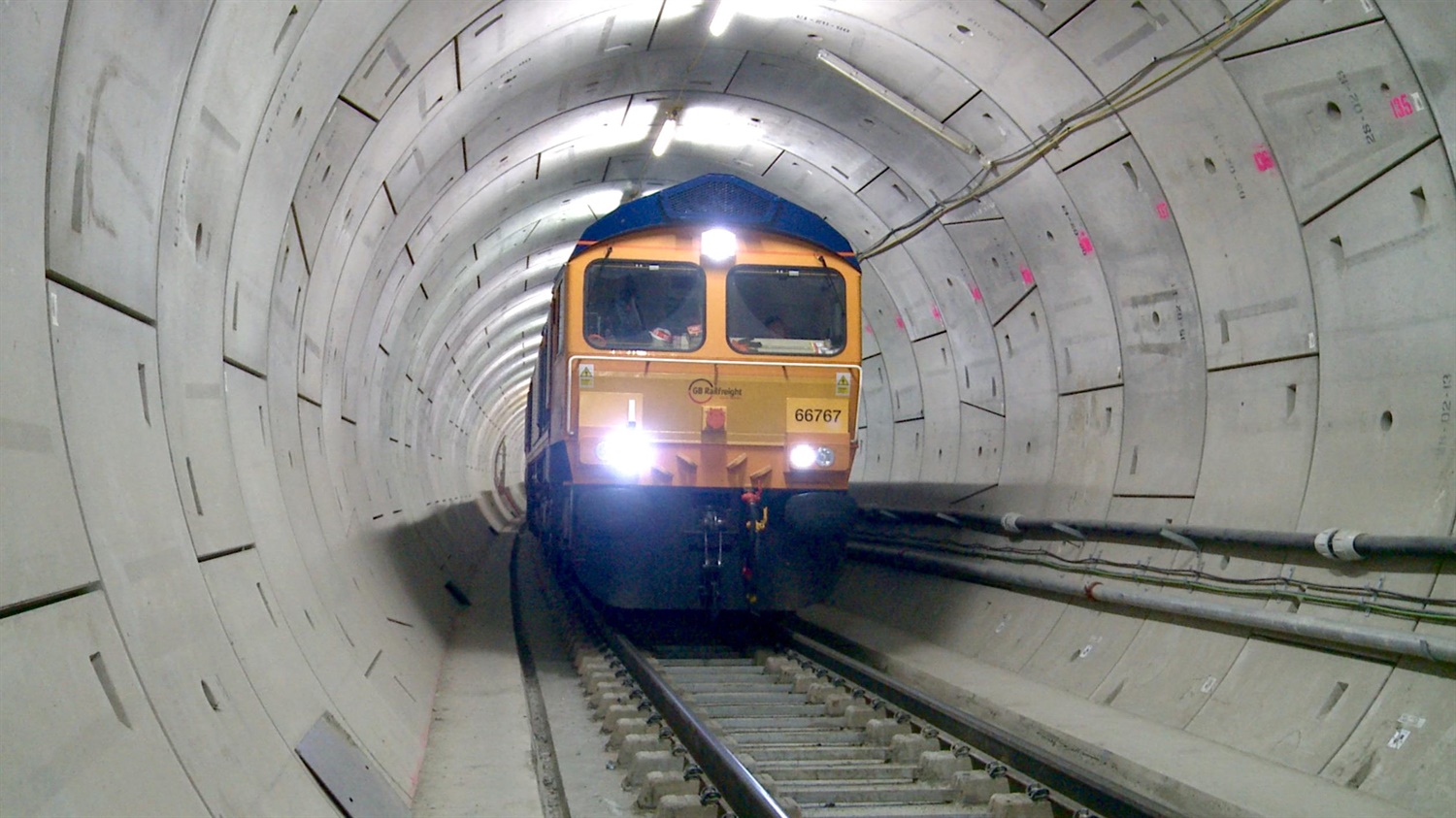
To install the standard slab track, the team is using a 465m-long concreting train, which is a sophisticated mobile underground concrete batching factory.
Brought to the UK from France in August 2015, the refurbished vehicle is based at Plumstead and at its peak production rate will be able to install 250m of concrete track slab per day.
“But we’ve been perfecting our methods of concreting as well,” said Purcell. “For instance, understanding how this concreting train works and what it can do, and what the output can be. One of the key lessons learned is that when we have a section of track ready, we make sure we only batch enough concrete for the slab we are going to cast. If we batch too much, it is just concrete we have to find a home for. And when you are 2-3km underground and you have concrete that is slowly going off – you don’t want that situation. You want the bare minimum.”
He added that a lot of time has been spent on making sure people understand how the quantities work, but the team is now in a strong position.
“We are trying to work ourselves into a pattern which delivers the outputs we need to deliver.”
Tell us what you think – have your say below or email [email protected]