01.03.15
‘A far superior weld’
Source: Rail Technology Magazine Feb/March 2015
Adam Hewitt went to see one of Network Rail’s new mobile flash butt welders in action, and heard from project manager Bob Hervey and others helping deliver the new service.
Back in 2012, RTM interviewed Network Rail’s mobile flash butt welding service leader Sean Heslop about the new technology being brought on board, based on a converted Doosan 170 with a new weld management system and welding head from Holland of Illinois.
30 months on, and real progress has been made in getting the new fleet of vehicles into active service, and in proving the remarkable claims made about their speed and the quality of their welds.
RTM was invited to the Rail Innovation & Development Centre (RIDC) at the High Marnham Test Track near Tuxford to see just what it could do. Stopwatch in hand, and in daytime conditions of around 8°C, the claims did prove accurate.
Learning lessons
Flash butt welding itself is not new, of course – it was introduced to the UK rail network in the 1990s, and technology from companies including Sersa, Plasser & Theurer and GrantRail/GrantWeld (now VolkerRail) has been used since.
But the new machines, when they were designed, “included all the lessons learned” from those older models, according to Network Rail’s project manager Bob Hervey.
The design of the knuckleboom and welding head even allows for ALO (adjacent line open) working under live overhead lines, by staying within gauge – though this functionality is not yet being used until there has been more evaluation by Network Rail’s E&P teams.
Hervey said: “That’s what it’s been designed for, though – so we can have this running as part of the seven-day railway, working in amongst running traffic. So far, we’ve always taken an isolation. It’s a big step for people to start using this equipment in those situations. From the safety side, we’ve designed it to the requirements to do ALO working under live overheads, and putting it into practice is somewhere we’re going to go.”
Simultaneous welding and stressing
One of the most important advances of this latest technology is the ability to do simultaneous welding and stressing of the rail, saving a huge amount of time.
Hervey explained: “We can complete the production welds and stress in the same shift. We’re reducing a whole shift for stressing.”
The machine, a Doosan DX170W wheeled excavator converted into a bespoke RRV for Network Rail by GOS Engineering in Blaenavon, South Wales, is fitted with the latest Holland K945 welding head and weld management system.
The computer has a useful display showing information during the weld, but more importantly collects a vast amount of data during each weld, which can then be analysed later – especially if there is a problem during production.
Modern method
The traditional method of welding has been aluminothermic welding, which requires a ‘filler’ material, resulting in a weaker weld, with a longer cooling and solidifying time.
Hervey said: “Flash butt welding, by contrast, is a solid phase weld – welding rail to rail with no filler material. It results in a far superior weld that is stronger in every way. It is better in terms of fatigue, and the flexibility of the material. There are no differential material issues and no hardness issues, because it’s exactly the same material. Because you don’t have to have a collar configuration, you’ve got a stronger weld. We can bend and flex it better, which is what we want for the rail.
“Even a bad flash butt weld will outperform a good thermic weld. It’s also much faster: we’re looking at a production rate of about four welds an hour.”
The weld uses basic electrical processes: using a short-circuit to create heat, then forging the metal together.
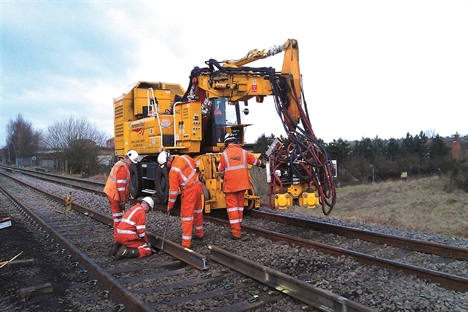
Culture change
Hervey has been doing flash butt welding for 16 years, so knows the process inside out, though he has also been an aluminothermic welder. He is clear that the new method is a real step forward, and although “with new technology comes the need for a culture change”, he said: “Going forwards, to have a seven-day railway, we’ve got to bring in new technology. We’ve got to remove the old aluminothermic welding: a tonne of equipment in the back of a van, two men carrying it, loading it on the track, pushing it down the track.”
Hervey said he and his ‘titanium knee’ are testament to the need to replace such hard, manual work with modern, speedy technology.
Forceful
The machine’s maximum amperage is about 1,000 amps, though during the weld cycle it is typically at 600-700 amps, reaching temperatures of 800-900°C.
Although it has a theoretical capability of pushing the rails together with 120 tonnes of force, typically it is more like 40 to 50 tonnes. Hervey explained: “When we stress, we’re going to use some tonnage from the machine’s 120-tonne capability to ‘pull’ the rail. We need to have at least 50-60 tonnes of force for that, so we have a margin of about 60 tonnes to do the weld.
“It depends on the ambient temperature. The colder it is, and the longer the pull, the more tonnage it’ll take to stretch it.
“Originally, we were [concentrating on] big long lengths of track, but what we’ve also found is that we can do the short lengths of track a lot faster. That means that in short possessions, we can do significant work.
“Traditionally, changing a defective rail with aluminothermic welding, the minimum would be two hours – because you’re doing a casting, you have to allow it to cool and solidify. With a flash butt weld, it’s only eight minutes before we can start doing all of the other work.”
The flexibility of the machine means it can be positioned on the track, on the adjacent track, lineside, in the four-foot, on the road, or even in the factory.
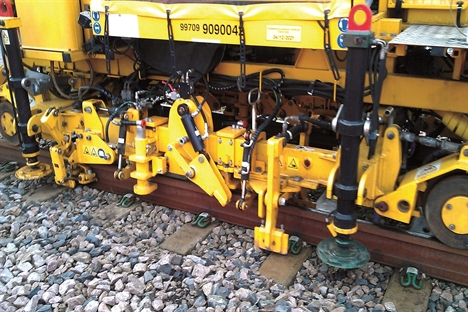
Turning the volume down
It has also won an award for its low noise impact. The old flash butt welders and generators used to exceed 120dB, but it’s now under 80dB, and less than that when on tick-over. This is important, when you consider that Network Rail treats as a “lineside neighbour” anyone who lives within 500 metres of a railway line – which amounts to one-third of the country.
RTM watched four different welds take place on the day we visited Hervey and his team, replicating different real-life applications of the technology.
As the sparks began to fly, Hervey said: “You can see the electrical current is going round the rail profile, warming it up. Then it will be forged together.
“Because we’re doing a cold weld, we can take this one off straight away. When we do a stress weld, we leave it for eight minutes, just to hold it.
“We can now put a train on that…we can do anything with it. There is no waiting time at all. That is your flash butt weld – did you see the speed of that?”
We did, and it was indeed impressive.
Stressing
For the stress weld, the machine itself pulls the rail towards the contact point – making for an impressive sight, as the entire rail ‘slides’ slowly past the clips. A video showing this is available on the RTM website.
Flash butt welding does, however, absorb some of the rail – 27mm to be precise. The old machines used to ‘forge to resistance’, where they would just keep pushing and the exact amount of material absorbed could not be known. More recently ‘forge to distance’ has been the rule – a concept that Hervey himself demonstrated on the same test track nine years ago.
The absorbed rail is forced and squeezed out of the top, with the resultant waste material (known as the upset) cleaned off with a shear blade.
Hervey said: “A ‘good’ upset has three layers. That tells you that each of the processes has been gone through and it’s forged nicely together, and the shear has left a nice clean quality weld.”
RTM saw that for ourselves, and also the process by which the rail is ‘bowed’ – the 27mm absorption means there is slightly too much rail (17mm, accounting for the 10mm gap), requiring a slight bowing of a section of the rail out of the housing, using a simple technology – scaffold poles. As the rail is pulled, welded and stressed, it snaps back into the correct position in the housing.
Calculations
Technician Lee Emmerson talked RTM through the calculations required for the pull, based on the linear thermal expansion coefficient of steel, the ambient temperature, the length of rail and so on.
His calculations are virtually spot on – 0.1mm out from the actual pull of 148.7mm, according to the weld management system.
He added: “If something does go wrong, you can use the data in the weld management system to analyse the graph and numbers and see exactly what went wrong and how, and at what point in the welding process.
“We keep picking up techniques, like today. As we find something better, we implement that into the system – it can only make us work quicker, and increases our production rate. We’re getting better and better as we’re going on.
“Ultimately, preparation is key. It is a lot quicker than aluminothermic welding, but it’s all about the preparation.”
Preparation takes longer if the machine is sitting on the same rail that is to be welded, because it takes slightly longer to ensure a good alignment.
Hervey said: “We’ve got hydrostatic drives underneath, so it’s self-propelling. The machine can turn itself around and drive the other way, and weld both ways, it’s 360-degree. It’ll work on the rubber [tyres], if we’re on the side of the track. I could drive it from the road, weld in the four-foot, put rails in outside the track during mid-week short possessions, weld it, come back, put the rail in, then do the re-laying. The flexibility is there.”
Although the machine can be used in most circumstances, it can’t where the rail cannot moved, such as the main part of S&C – because of the necessity of absorbing some material from the rail.
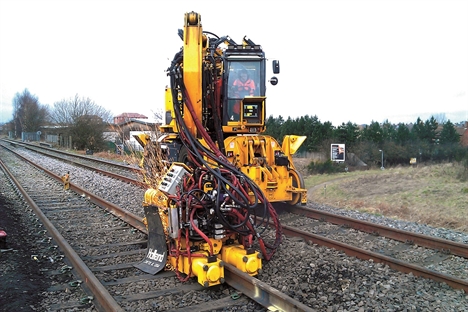
‘By Network Rail, for Network Rail’
Network Rail made the proactive decision to run its own mobile flash butt welding service – not to buy one in.
Hervey told us: “This equipment is designed by Network Rail, for Network Rail, operated by Network Rail. I think that’s the future. All too many times we’ve used contractors and relied on other people – that comes from the old Railtrack days, using other companies or contractors to bring in that technology. Ultimately, doing it this way reduces costs.
“Everybody’s a customer or potential customer – High Output, Infrastructure Projects, individual delivery units.”
Technician Nathan Astin talked about this in a recent feature in Network Rail’s staff magazine, saying: “On a day-to-day basis, my customer is likely to be a maintenance department or a renewals or CAPEX team. It could just as easily be an independent rail provider too. We could offer our services to other companies – and not just in the UK. In theory our customer could be global.”
Hervey continued: “At the moment, we’re a new technology, and as with any innovation, some people want to use it straight away, while others want to stand back. In the past, we’ve had people trying to shoehorn our technology into their old methods, and that doesn’t work either.”
Currently, all four of the active machines are based out of York, but this should change once all 10 are online. The original plan as described to RTM in 2012 was to also have them based at Whitemoor, Rugby and Eastleigh, as well as York. There are currently 70 men making up the service, recruited not just on technical ability but on work ethic – Hervey said that despite the technology and machinery involved, mobile flash butt welding is a difficult job, with few opportunities for rests and breaks, compared to other track jobs. The team is made up of many contract welders, plus a large ex-Army contingent, Hervey told us.
The approvals process for the machines, both the RRV element and the welding head element, has been thorough – some might say slow – but Hervey said it is important to be absolutely sure. “When we let these machines go, they can make a lot of welds very quickly, and if we have any technical issues, we’d be having to take out a lot of welds. We’ve had that in the past – we’ve maybe run before we can walk. But a lot of the learning curve has been done now.”
Tell us what you think – have your say below or email [email protected]