29.08.18
Going global: an interview with Network Rail’s Leevan Finney
Source: RTM Aug/Sept 2018
RTM’s Jack Donnelly sat down with one of the leading minds behind Network Rail’s most advanced and innovative rail maintenance technology so far. Director of fleet and engineering Leevan Finney (pictured) talks about the project, the impact it will have, and how it signals the way ahead for the organisation.
When you’re a director at the Route Services team at Network Rail, rail maintenance is your bread and butter. So for Leevan Finney, the director of fleet and engineering who has been at the company for almost a decade, the department’s latest flagship project will look to push the boundaries by providing the most efficient and reliable rail maintenance model the company has ever seen.
The HSM-R-B rail milling train, produced by German company Schweerbau, is an unprecedented advancement in rail services technology for Network Rail, which previously used road-rail vehicles for track maintenance. The 190-tonne brute, dubbed the “milling machine of the next generation” by the vehicle’s Stadthagen-based manufacturer, will target defects in the rail head by removing a layer of its metal – leaving a smooth running surface to profile without the need to close the track, and resulting in effortless maintenance works for staff on the lines.
Finney said that Network Rail had considered using grinding trains – a similar set of equipment which shaves off a top layer of deformed or cracked rail before it moves down into the lower parts of the rail material – but felt the machine would not provide as much value for money. “When you’re doing that, you are tying up that big grinding train that can work at high speed to a very short section of track,” he said.
“It’s almost like buying an articulated lorry to go to your nearest shop – and that really isn’t good value for the machine. We introduced the milling train because milling will take off a lot more metal at a much slower speed, but it can do it in a single pass – so the cost of that compared to doing multiple passes is a lot less. You also save a lot of time and pick up 99.9% of the debris, so it’s less likely to cause an infrastructure issue.”
The milling vehicle runs two milling heads per rail, per train, and will operate as a duplex unit, allowing for four milling heads per rail. Not only this, but the machine can also mill around 5km an hour using new automated technology that allows it to change milling tools, improving safety by reducing the need for highly-skilled staff members to work near the damaged track.
Leevan explained: “The new trains have the ability to negotiate themselves around the rail condition: before you would be reliant on a very highly-skilled individual in a cab visually checking the rail. Whilst this still happens today, the computer technology in real time will now say ‘well, if you do this, it’s this much better.’ So the individual can now make the decision on a much more intuitive system, meaning there is less opportunity for incidents to occur, so it’s less likely that the track will be closed, which leads to an increase in safety.”
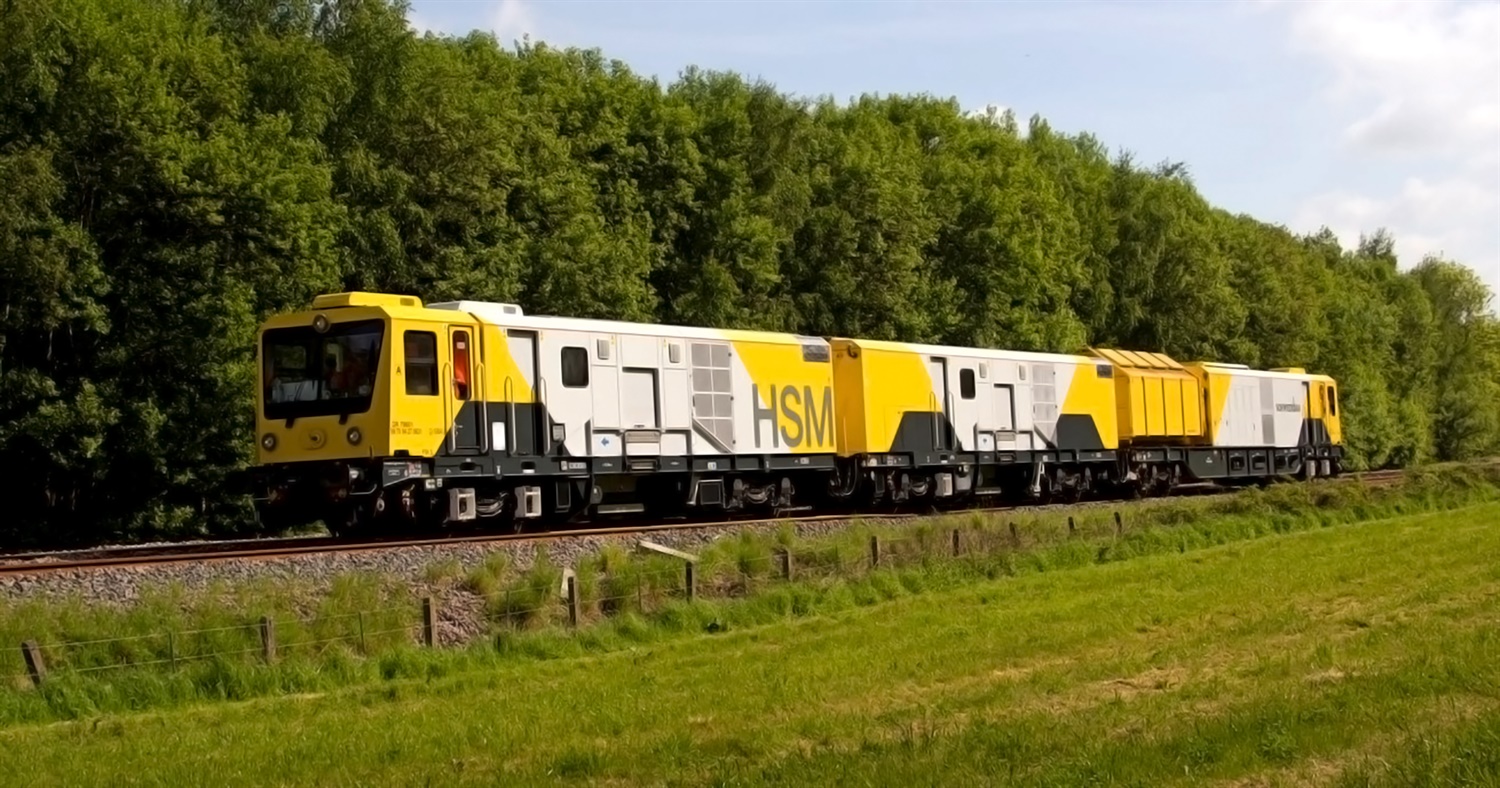
Expectations vs. reality
The newest project from the Route Services department signals exciting times to come for Network Rail. But for Leevan, one of the leading minds behind the equipment, how do the latest advancements in rail technology compare to those when he first joined the industry?
Born in Stoke-on-Trent in 1984, the proud Potter Leevan first started working in the construction industry for local company JC Bamford Excavations until 2009, when he was attracted to the rail sector to work as part of the vehicle acceptance team for Network Rail.
“A number of my colleagues had moved to Network Rail and shared their experiences in moving into the rail industry and how it was different,” said Finney.
“It was more dynamic; there was a perception that the rail industry was a niche industry, and that was shared and seen as specific and limited to what you go into. But having spoken to my colleagues, I started to get the feeling that there was something different and that there was something out there.”
When he joined the company, he was amazed by the range of opportunities and progression that had opened up for him: “I wasn’t aware that Network Rail had this vast array of careers and opportunity with a whole supply chain that supported it, and was absolutely symbiotic. You could do whatever you want – whether it was communications, marketing, commercial, pure engineering, or even train driving. The rail industry can offer a job to anyone, as I see it, in the UK.”
Progressing through various roles in the company, the 33-year-old eventually took up his latest role as director of fleet and engineering for Route Services. Leevan said it is the diverse range of skillsets and backgrounds of his workforce that shape the quality and standard of the department’s output the way it is today.
“One of the biggest benefits of the rail industry for me is the diversity of people. Allowing people to think and perform differently is a real key aspect of our progress,” he told me.
It’s not just its own staff backgrounds from which Network Rail sources inspiration for new projects, either: Leevan said the company looks worldwide and in different industries to identify where it can improve services for passengers – and rail milling, used frequently to maintain railways in Germany, is a great example of this.
“I would describe Network Rail as a worldwide company – because we have a lot of touchpoints, whether it be European, whether it be in the US, whether it even be Australian,” said the fleet and engineering boss.
He added: “We have met with railway companies in Germany to see how they treat their tracks: they use milling and grinding very differently to how we do it in the UK.
“They do that because they have a very different and unique set of challenges they need to address within a different system, but we’re still providing the same kind of output. Sitting together in that process means we can gain by looking at things differently, and they get something out of it as well – and it brings us closer together.”
Leevan also highlighted the technocentric direction from the company, focusing on how they can take inspiration from environmentally-friendly modes of transport, such as the Tesla car, and implement this in the UK’s rail industry. He said: “We always have to balance those against the funding that we have available – but I think that as we move forward and get cuter to how we can apply technologies such as the battery-powered car, and put them into our trains, then that is where technology will move forward.
“Those things that Network Rail has never stopped me nor the team from doing is something I really think we should seize. Where we can use that knowledge to drive value for the rail industry, we absolutely have to.”
With the director from Stoke-on-Trent taking inspiration from Europe, North America and beyond, the milling train truly encapsulates a modern, worldwide approach from Network Rail. With CP6 on the horizon, the diverse culture from the company will shape the UK rail industry both now and in the future.
TELL US WHAT YOU THINK
[email protected]